Technologies
Aoki’s research and development
Aoki’s research and development
Aoki’s ever-evolving technology
We are always on the lookout for further possibilities for improving and driving the evolution of containers.
We will never relax our research and development efforts to leverage the characteristics of different materials, create functional shapes that enhance everyday convenience, and enable containers to be molded with less energy. We firmly believe that further developing our unique molding technology will help make life safer, more convenient, and more comfortable for people throughout the world.
Aoki’s research and development
Technology development
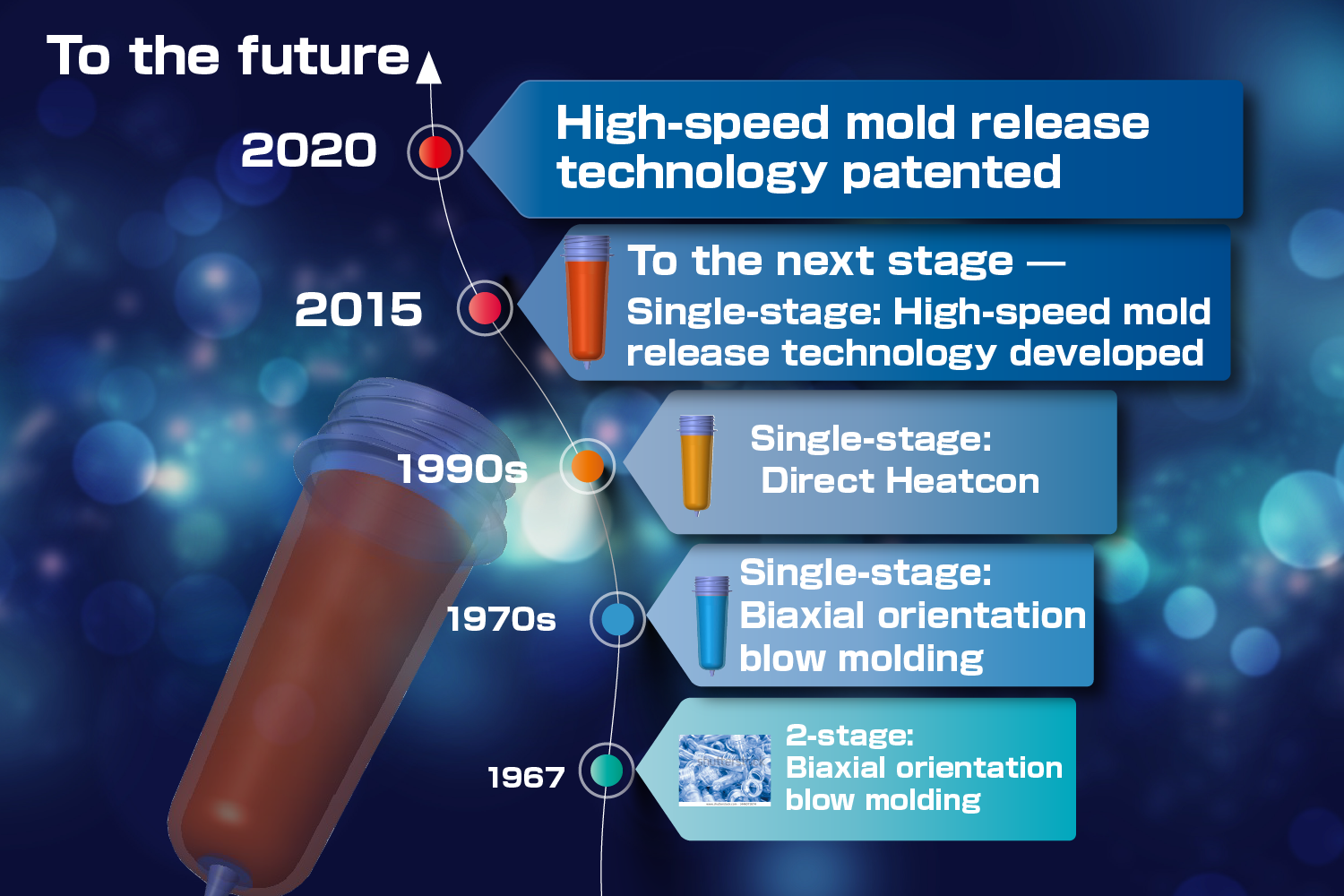
High-speed mold release technology, further evolution of Aoki’s unique molding method
Over-engineered molded products and cycles involving excessive time and energy are common in conventional stretch blow molding (high stretch ratio, high air pressure/biaxial stretching). Aoki developed its high-speed mold release technology to resolve these issues. This proprietary Aoki molding method enables much higher cycle molding than previously with the same number of cavities and same weight.
Our high-speed mold release technology is now spawning success stories throughout the world.
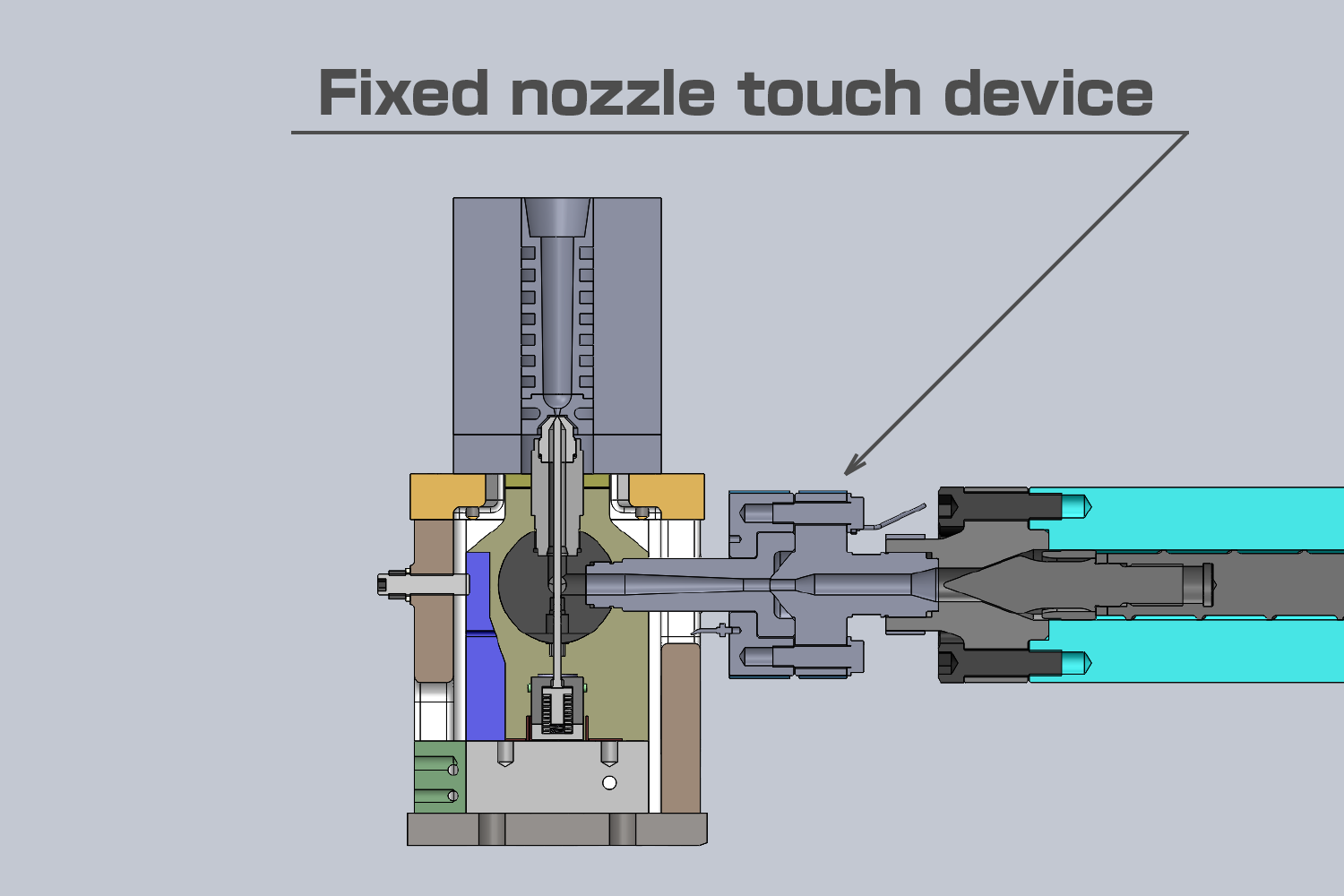
Fixed nozzle touch device, a high-performance component for improving productivity
Since our founding, we have relentlessly improved and enhanced our products in line with our basic philosophy, with a sense of purpose and ideas that remain unchanged even with changing times. We seek to shave even 1/100th of a second off cycle times, and fixed nozzle touch is one of the innovations to emerge from our pursuit of that goal. (Patent obtained in 2019)
This is a high precision component that can help resolve various customer issues. Don’t hesitate to contact us to learn more.
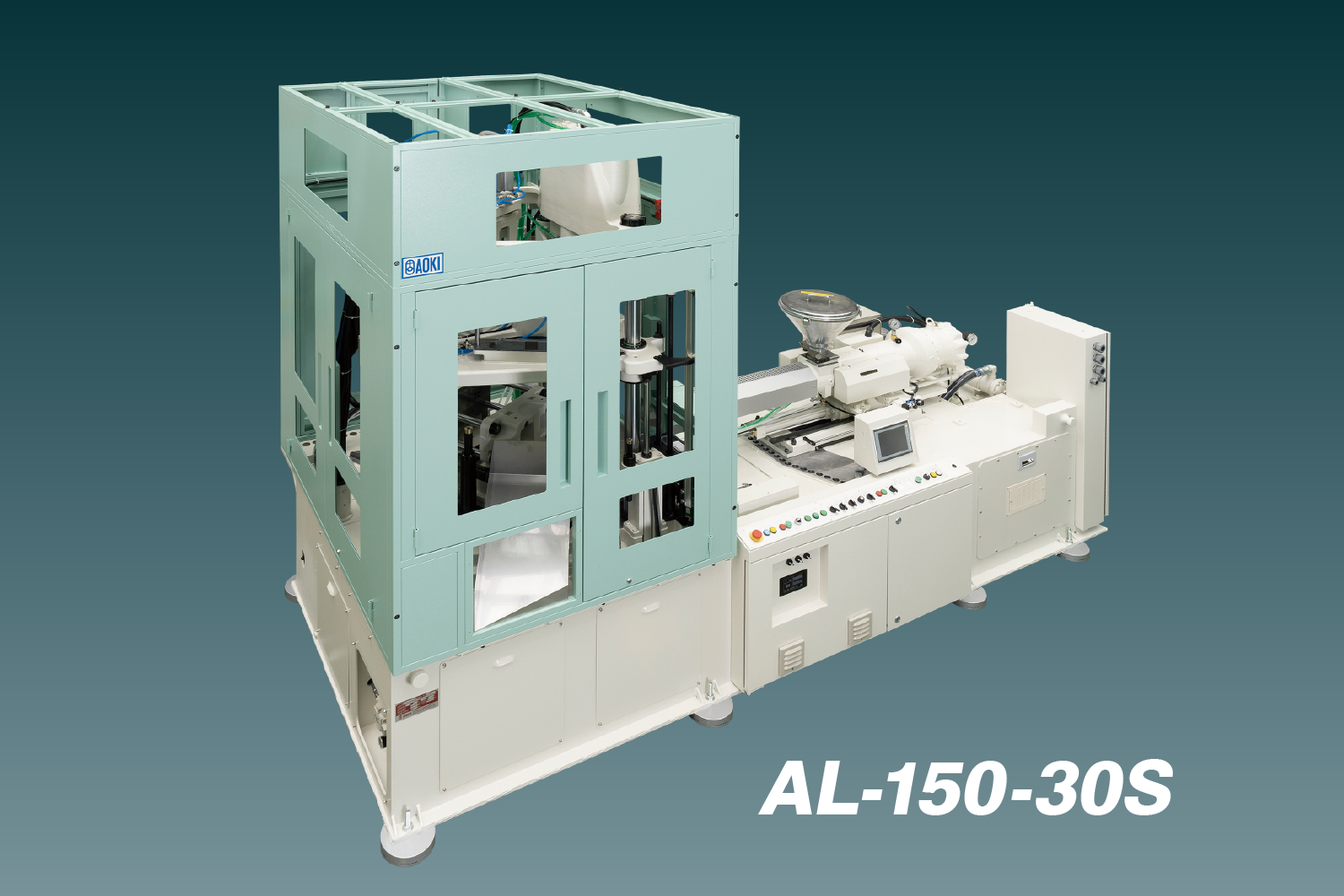
AL-150-30S, the little giant
This machine is designed not only as a high-cycle version of the 100 series for high-mix, low-volume production of molded products up to 240 mm in total length, but also for downsizing from the AL-250LL-50S entry model. At the same time, it is equipped with a rotation speed control system, which reduces electricity consumption by 40% compared to the AL-100L-20. This is an extremely versatile machine that hits the spot whether you are wanting to mold large* or small containers. (* Sizes that the 100L-20 cannot cater to)
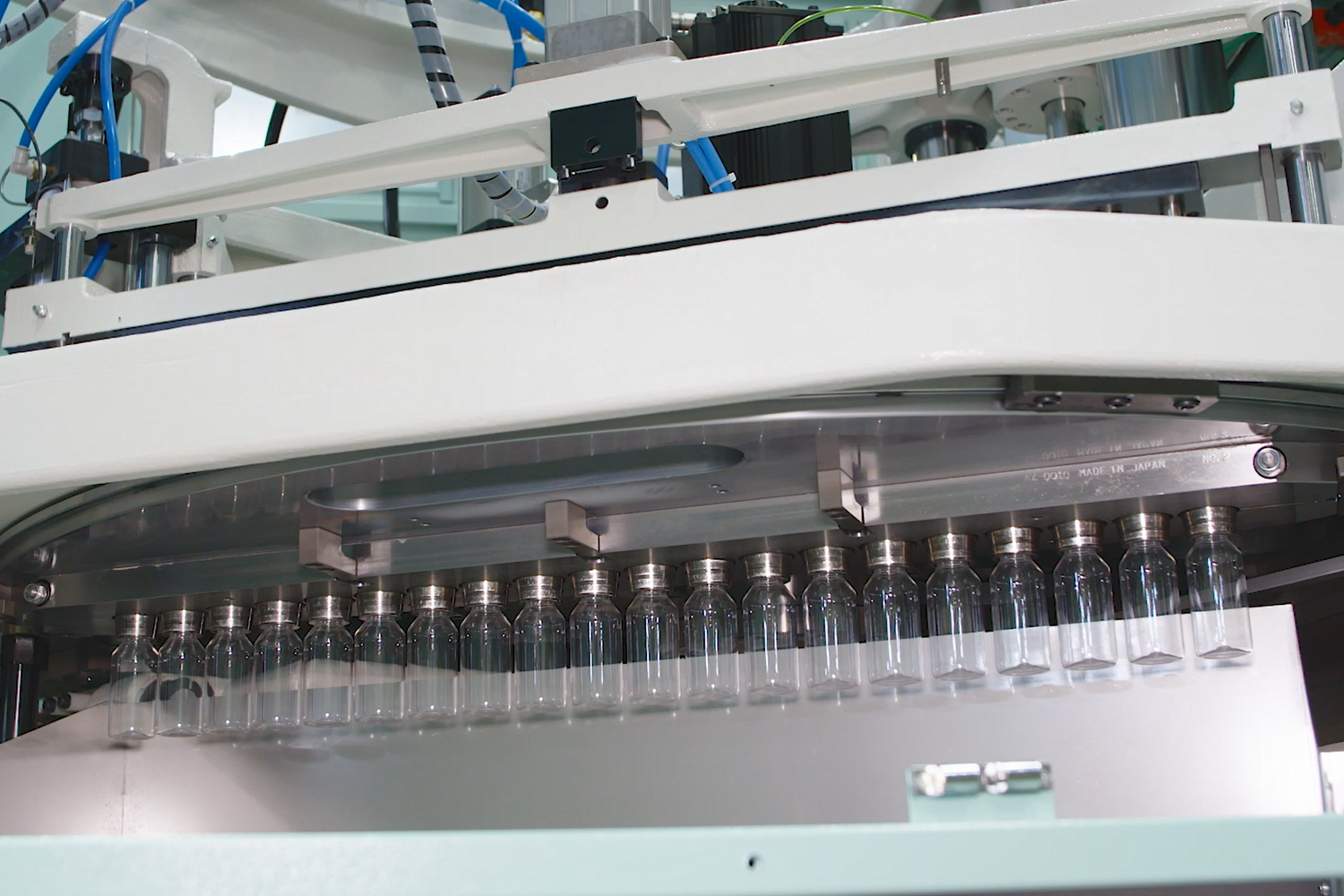
AL-1000-60, a new model born from “minus invention” concepts
This new model has a simpler system than the SBIII-500N-60, our former flagship model for molding small containers. The AL-1000-60 further improves productivity and support for different materials. The 500N-60 model used 2-row molds, but the AL-1000-60 delivers higher productivity with just one row. This simpler structure improves production stability, product quality, and workability for maintenance and mold changeover.
Advantage 1: Much shorter cycle — reduction of processes from 8 to 6
Advantage 2: Simpler structure
(1) Mold changed from 2 to 1 row
(2) Improved production stability and product quality
(3) Improved workability for maintenance and mold changeover
Advantage 3: Wide range of materials supported through use of high-speed mold release technology
This model can handle PP, HDPE and other materials in addition to PET, thereby expanding the potential of single-stage molding. It is a new model that is capable of mass-producing containers owing to its shorter cycle while at the same time being a special purpose machine for molding small containers.
Aoki’s research and development
Aoki’s container molding technology
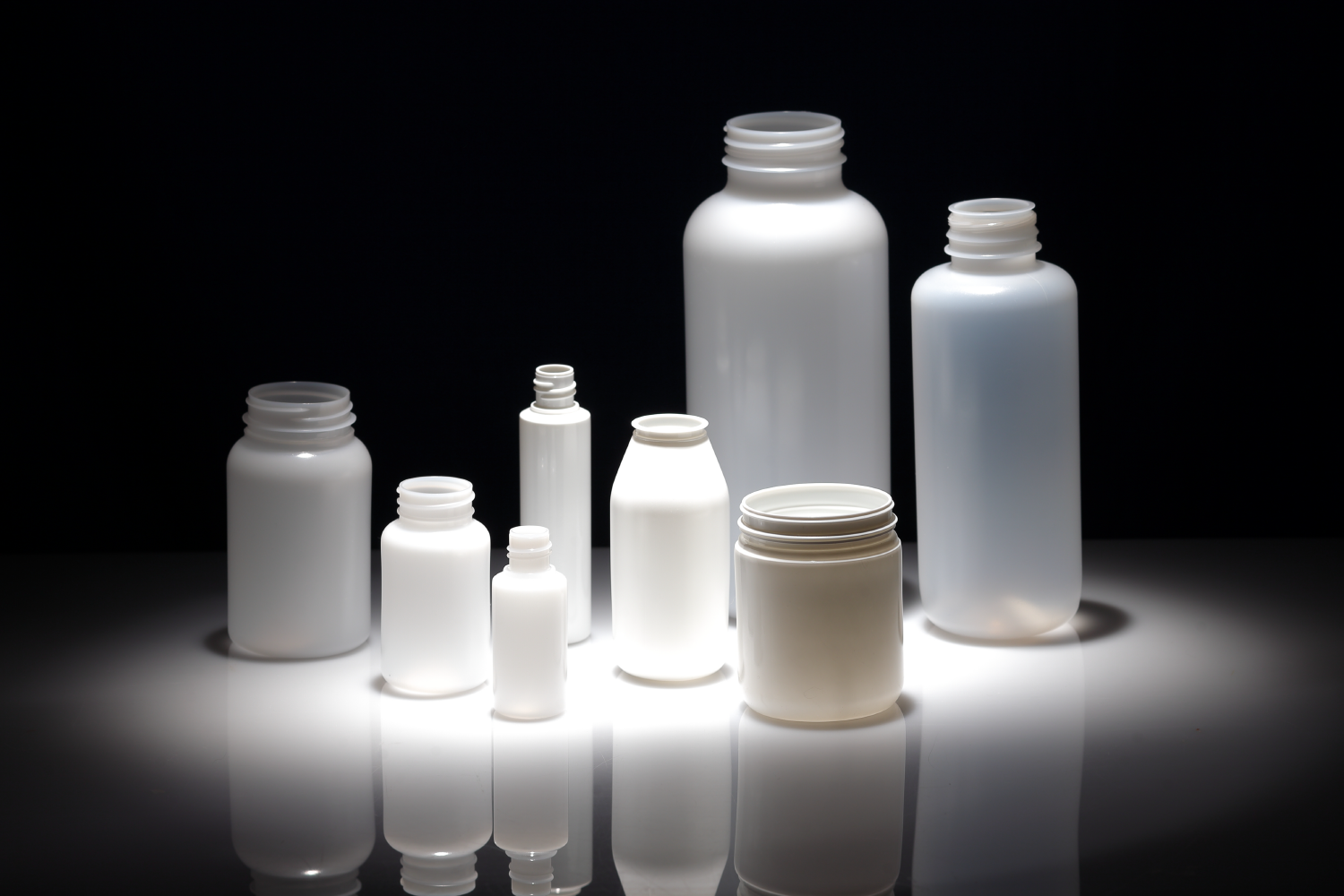
Aoki’s patented technology* driving evolution in HDPE molding (* Patent obtained in 2020)
With conventional polyethylene molding technology, the injection mold for preform molding had to be heated to avoid various issues, inevitably prolonging the molding cycle. Our new polyethylene molding technology (patented) uses our high-speed mold release technology and rapidly blows the preforms after mold release to dramatically shorten the molding cycle time and mold high quality containers.
This gives customers even greater choice.
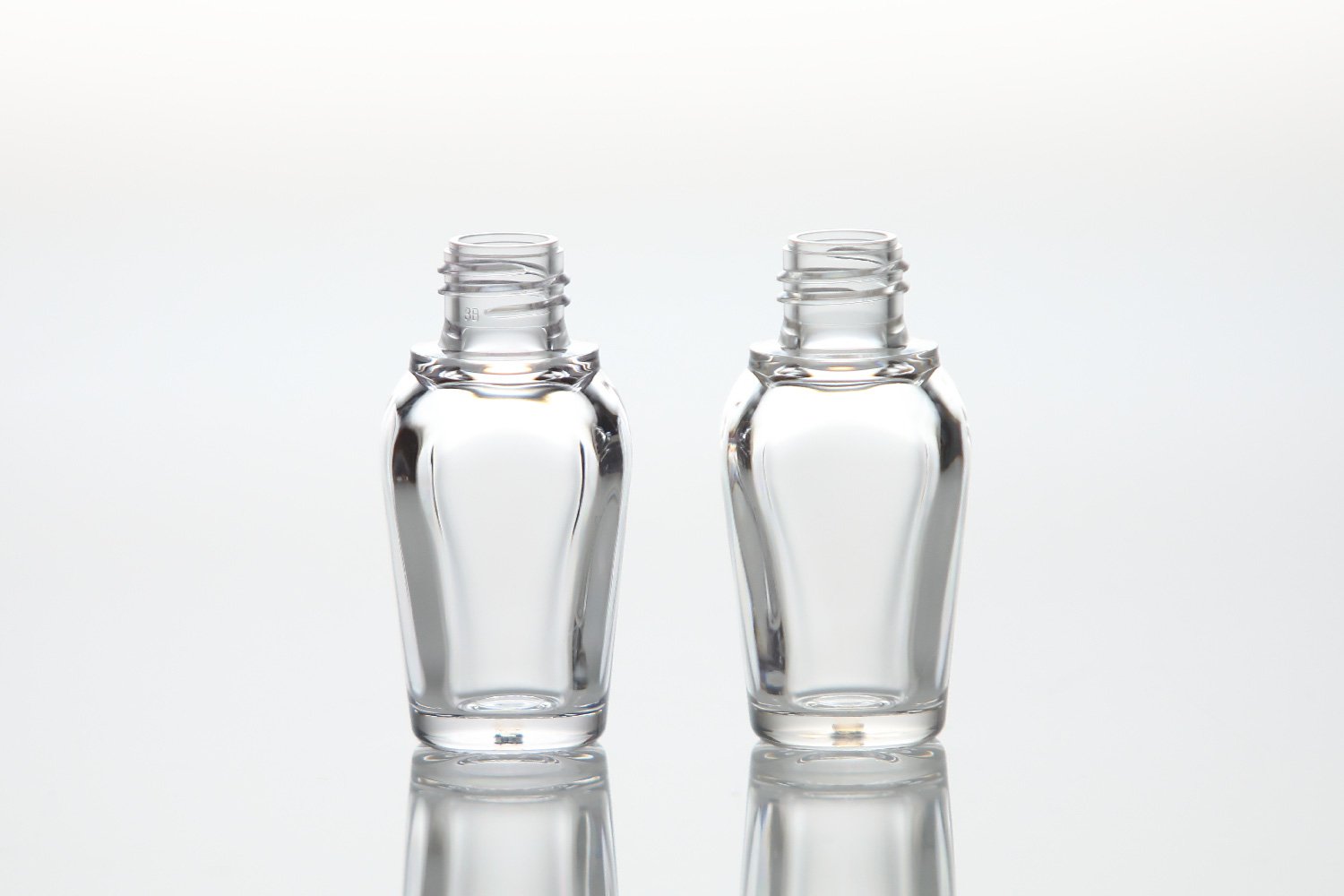
Machine model — Before: SBIII-250LL-50S 35 sec, After: AL-500L-50S 13.8 sec
PET-G and PCTA are often used to give cosmetic bottles and other thick-walled containers a high-end transparency, but Aoki’s high-speed mold release technology enables the molding of glass-like containers at shorter cycle times with no crystallization even using ordinary PET.
Machine model:
Before: SBIII-250LL-50S 35 sec
After: AL-500L-50S 13.8 sec
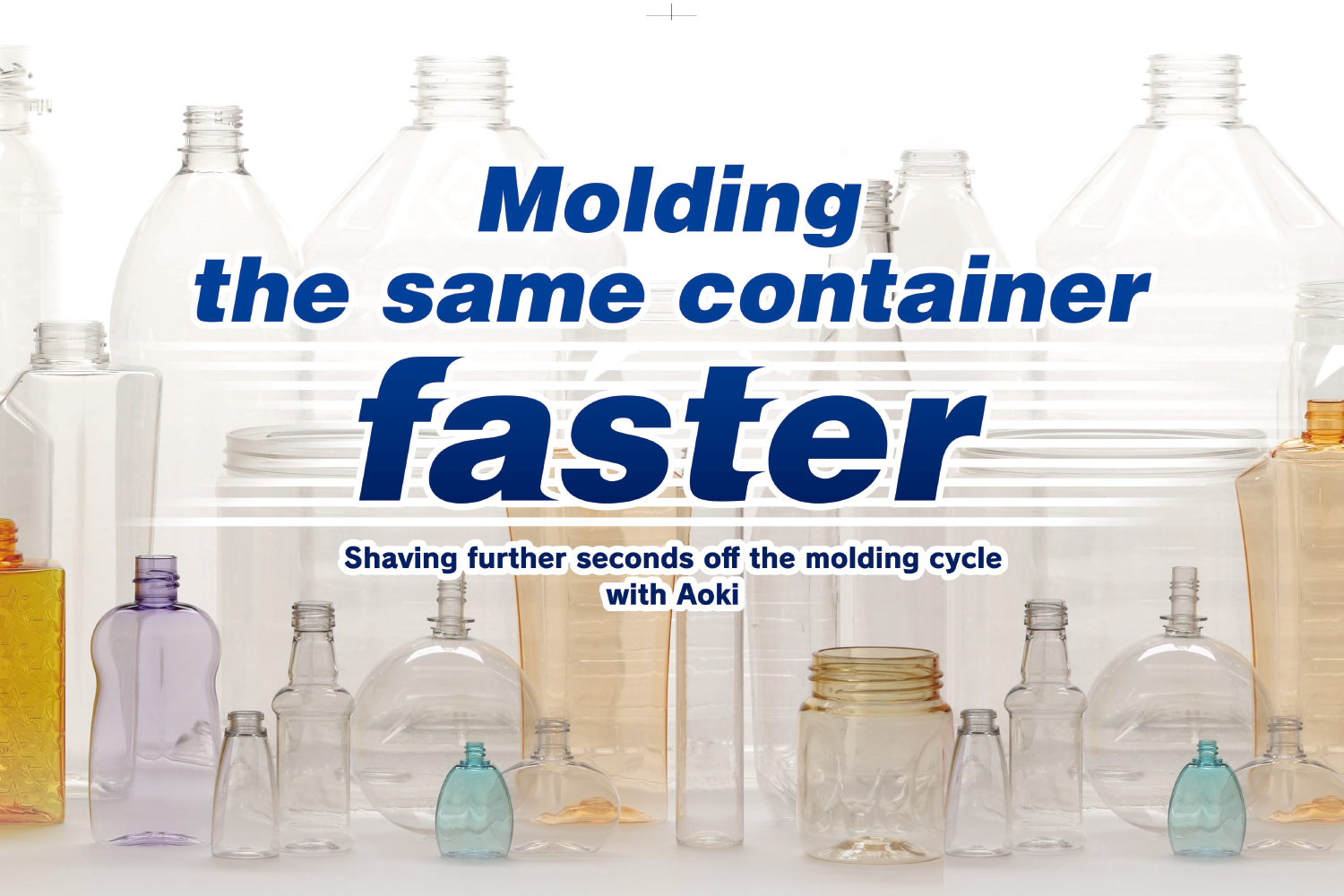
Molding the same container faster
Is lightweighting the only way to “produce containers with minimum expenditure of time and energy”? Aoki's answer is to enable the same container to be molded faster.
Enabling containers of the same shape and weight to be molded faster than ever before has various advantages. For example, speeding up the molding cycle by 10% means 10% more containers produced per hour, effectively increasing product value.
Advantages
・Lower production energy costs
・Shorter production time and more effective use of human resources
・Molding machine downsizing possibilities
・Increased production even with older machines
Technologies
Aoki’s molding method
Molding containers from material at highest speed worldwide
Aoki’s unique molding method
Key technology: Direct Heatcon
Enabling single-stage 3-station molding, the ultimate simple mechanism, with Aoki’s unique molding method
Aoki’s research and development
Case studies
Inquiries about molding machines and container development
Molding machines Please feel free to contact us if you are considering deploying molding machines or producing containers yourself.